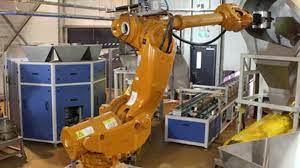
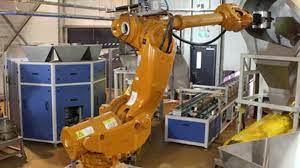
KEY BENEFIT
KEY BENEFIT
- Improved ergonomics, health and safety
- Reduced operational costs
- Quicker turnaround times
- Enhanced quality
- Reliability of supply
Innovating for quality, safety and productivity
We recognise that tonnage throughput remains a prime objective for many iron ore producers. However, it needs to be done without risking productivity, quality, cost or safety. Many miners, port operators and steel producers are looking to automate their sampling and laboratory analysis processes to help solve these challenges.
WHAT WE OFFER
Automated solutions designed to enhance quality and reduce risk
Well over two billion tonnes of iron ore is mined every year, often involving multiple handling stages, beneficiation, stockpiling, blending, and shipping over vast distances. How can you be certain of the value of your ore during all these processes?
You need to ensure that the samples extracted and prepared along the entire value chain are representative so that meaningful decisions can be made based on their analyses. If you get this wrong, you face the potential of losing millions of dollars in terms of:
- Poor investment decisions
- Poor estimates of ore reserves/resources
- Poor utilisation/wasted resources
- Reduced mine life
- Poor plant performance or port inefficiencies
- Poor product quality
- Reduced income from product sales
You need analytical results that you can trust. However, with increasing demands for higher sample capacity, mass and quality, it is clear that manual sample preparation and analysis laboratory operations are falling behind, often due to the inability to rely on workers to provide a continuous, repeatable and unaffected process.
Recognising these challenges, we offer a range of automated solutions and equipment, designed to establish a standard that you can rely on. Our proven handling, sample preparation and analytical equipment, integrated with state-of-the-art software packages, is globally recognised as the most efficient solution for automating iron ore mine and port laboratories.
These systems are designed to run 24/7 for 365 days a year, immediately increasing sample capacity and improving turnaround times. Workplace ergonomics are also improved, as operators are not exposed to hazards, and the dependence on labour availability – often in remote locations – is reduced.
Automating these processes also delivers greater consistency, traceability and reproducibility, resulting in enhanced quality that you can trust. Our equipment can automate a range of common functions, including:
- Sampling and sub-sampling
- Sample transport
- Bar-code reading and RFID tracking
- Sample drying
- Crushing and splitting
- Pulverising
- Compiling and bagging composite samples
- Physical analysis – particle size, density and moisture content
- Fusion of pulverised samples into glass beads for XRF analysis
- Pressing pellets for XRF analysis
- Chemical analysis – XRF, TGA/LOI, titrations and wet chemistry
- XRD, FTIR and FTNIR analysis
Using our automated solutions, you will see long-term benefits, placing you in an improved competitive position within the industry. This is due to reduced variability, decreased bias, full traceability, increased mine life, and greater reliability of supply.
Confidence in the value of your product – from the mine to market – is critical to your operation’s success. High quality and proven automated sampling, preparation and analysis provide that assurance.