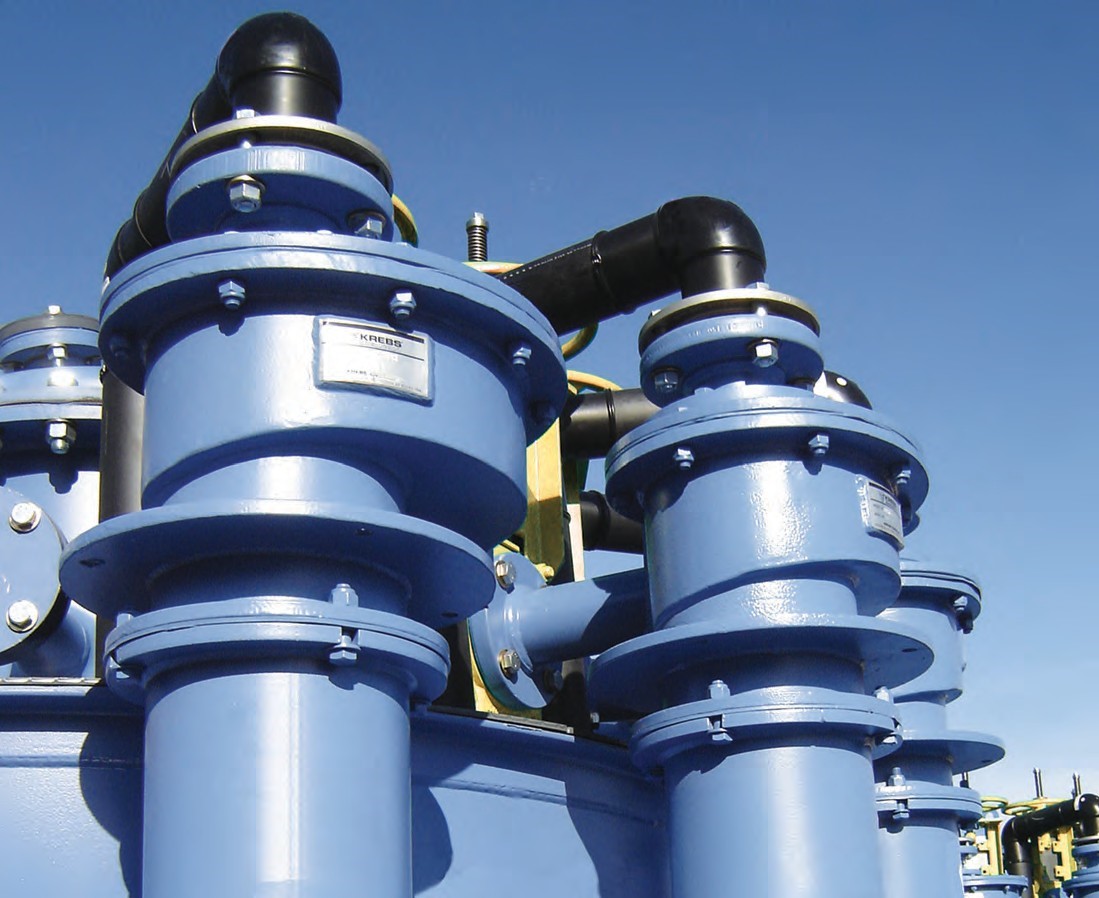
KREBS® gMAX® Cyclones
gMAX® Hydrocyclones : Finer particle separation with patented technology
gMAX® Hydrocyclone performance
We have dramatically enhanced hydrocyclone geometry and materials of construction to provide our customers with finer and sharper separations, as well as higher throughput, reliability, and product life. This improvement in performance and availability increases user’s productivity.
Key benefits
- Finer, sharper particle separations at high capacities
- Fewer cyclones needed for optimal performance
- Operates at higher feed densities for same separation results
- Operates at low cyclone inlet pressure
-
Retrofitted into existing installations to boost throughput
KREBS® Hydrocyclone technology leads the way in separation mining and industrial applications
Optimum cyclone performance relies on minimizing turbulence while maximizing tangential velocity. The gMAX® cyclone focuses on these two important factors, significantly advancing cyclone performance.
To achieve these two design criteria, the gMAX incorporates performance-enhancing improvements to the inlet head, cylinder section, cones, and apex. In fact, the performance level reached by the gMAX was once only achievable using many small-diameter cyclones, at a much higher capital cost.
■ Minerals processing
■ Oil sands
■ Power plants (FGD)
■ Chemicals
■ Automotive
■ Industrial and manufacturing
■ Water treatment
gMAX inlet head
- Contoured ramped inlet pre-classifies feed and reduces turbulence
- Reduced turbulence minimizes coarse solids bypass to overflow
- Less turbulence reduces wear
gMAX® Innovative hydrocyclone design
Inlet head design
The innovative gMAX® inlet design provides finer and sharper par- ticle separation at high capacities. Our commitment to continuous improvement in separation technology for our mining and industrial customers is why we are the world leader in cyclones.
The outer wall involute design entrance pre-classifies the feed solids prior to entering the main body of the cyclone. The inlet head of the gMAX also includes an improved vortex finder and top cover plate liner design.
These improvements result in reduced misplacement of material to the overflow and dramatically increased wear life. By using premium ceramics in the lower section of the cyclone, we’ve boosted overall wear life, greatly increasing the intervals between complete cyclone rebuilds.
inlet head design, layers of paint in different colors were applied to the gMAX inlet head liner (left insert) and to a competitor’s outer wall tangential inlet head liner (right insert). The components were assembled onto cyclones and slurry was pumped through them in FLSmidth Krebs’ cyclone laboratory.
The resulting wear patterns show a dramatic reduction and wear as a result of the improved gMAX geometry.
Cone design
Through the use of computational fluid dynamics (CFD) analysis, our gMAX cyclone design features more sharply angled upper cones, followed by longer, angled lower cones.
This combination maximizes tangential velocity in the upper part of the cyclone. It also provides a long residence time in the critical separation zones in the lower part of the cyclone. The result is
a substantially finer separation, with fewer fines in the underflow and less coarse material bypass to overflow.
World-class service and hydrocyclone test facilities
Our unparalleled technical staff of experienced engineers will quickly and thoroughly evaluate your potential applications and provide detailed recommendations and performance estimates. If your application requires validation testing, our hydrocyclone test lab can provide prompt testing at low cost. We also can arrange to run test cyclones at your site.
Optional liner materials available
- BPC rubber
- Neoprene
- Nitrile
- Chlorobutyl
- Alumina
- Nitride bonded silicon carbide ceramic
- Reaction bonded silicon carbide ceramic
- Sintered alpha silicon carbide ceramic
Fabricated/cast/molded unlined cyclone materials
■ 304L/316L SS
■ Duplex 2205
■ CD4MCU
■ Monel
■ Inconel
■ Nickel
■ Hastelloy
■ Other metal alloys
■ Polyurethane*